Webinar: Empowering People, Enhancing Performance
27th March 2024
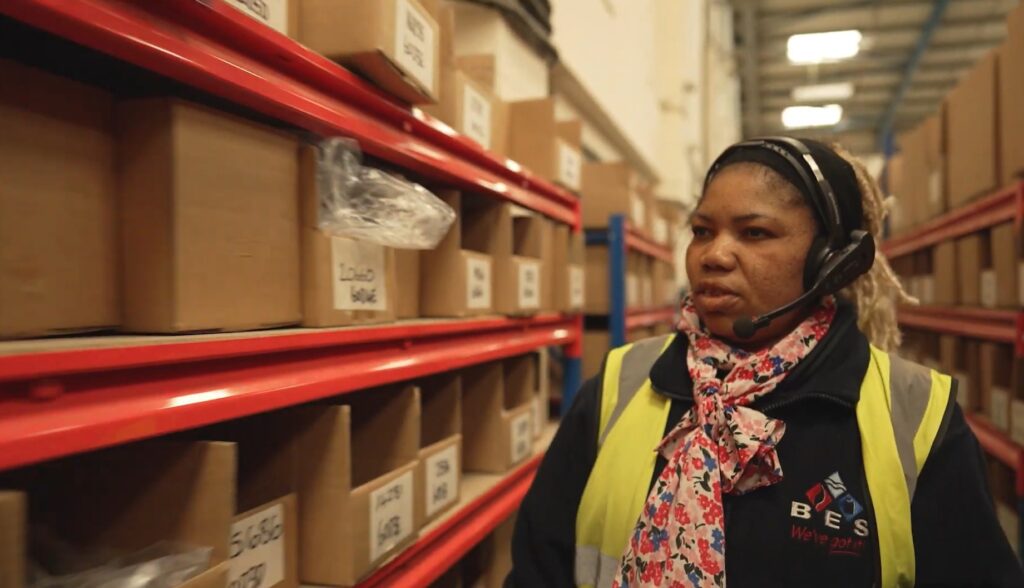
A new Webinar from Logistics Business is now available to watch on-demand. In association with Koerber Supply Chain and BES, Editor Peter MacLeod talks to Alex Parkinson, Business Analyst at Koerber about a warehouse upgrade project for BES in Birmingham. BES Operations Manager Steve Standley explains the before and after set-up for picking and ecommerce and what benefits automation, WMS and voice tech have brought.
BES are a plumbing, gas and heating trade supplier selling products and brands ranging from Bosch tools to Danfoss thermostats, Grohe taps to Grundfos pumps, Triton showers to Bostik glue. This inventory, in a 80,000 sq. ft. DC in central Birmingham, with 15000 SKUs and 1500 orders per day is a challenge in terms of suitable storage, picking and despatch. The company went from a paper-based operation to an automated voice and WMS solution in a project with Koerber Supply Chain.
The key benefits were:
• 15% reduction in total staff hours used
• 43% increase in productivity
• 88% reduction in training time for new staff
• 50% reduction in staff needed to check orders after picking
• 5 tonnes of paper saved per year (750,000 sheets) + printing costs
• Pick-up times on collection orders reduced to 30 minutes
Flexible Solution Required
“We brought technology to the workplace,” Operations Manager Steve Standley says. BES is a 45-year-old company and ecommerce took-off during covid. “Initially, for the extra orders, we just hired more staff. But that made us top-heavy for pick and pack. We needed to speed up and possibly reduce the head count,” he explains. The old system saw orders generate two copies of every despatch note. One went round the warehouse and one to the customer. There was a lot of walking involved as staff went round the facility to find and collect each item for an order. Having automated these processes considerable efficiencies have been made. BES upped staff pay and amended hours as well.
“It was a bit chicken and egg,” Standley says. “Should we introduce technology first or introduce efficient practises?” A new picking solution was required to help with the additional volumes. Installation, which commenced in March 2023 and was completed last August, needed to be done whilst order numbers continued to grow. “Testing was straightforward. Training is easy. Showing new starters the aisle and stock locations is the main thing.”
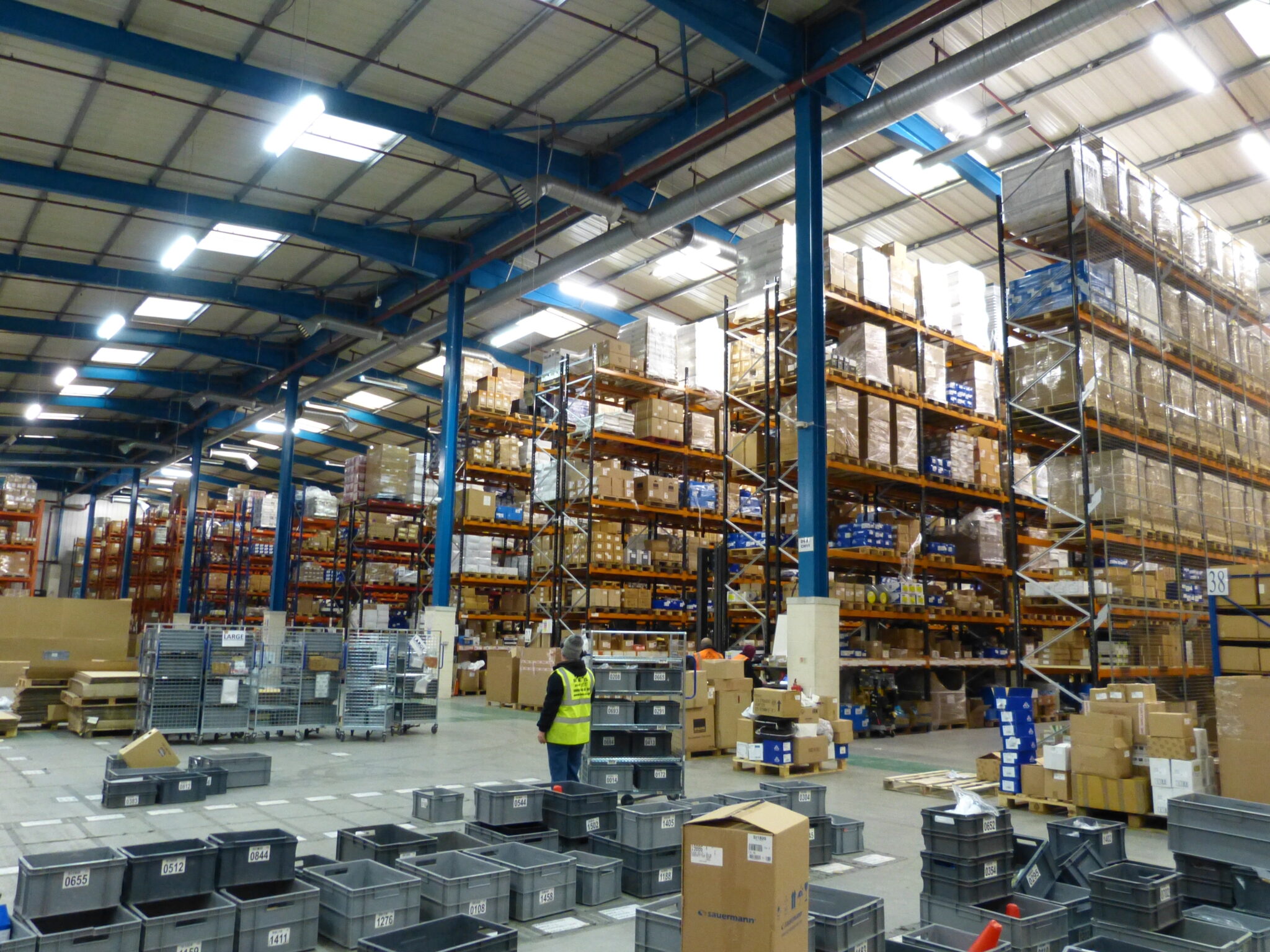
Empowering People
Major customers order in big quantities. Plumbers purchase parts for regular jobs. Consumers buy items for home delivery. BES ship via DX for odd sized and large products (overnight via the DX network), DPD for regular parcels and Royal Mail for items under 2kg. The decision was made to divide the DC into four zones, accordingly, from bulk down to small, plus a VIP area. Workers now wheel a roll cage of small or medium totes to the appropriate zone to pick into up to 20 totes at a time, before returning to the loading area.
Order Prioritisation
Another challenge for the upgrade project was to reduce the time taken to pick items meant for collection by customers on-site to be halved, to just 30 minutes. Instead of printed orders being sifted through, the new picking system recognises the warehouse’s own postcode as the destination. “It then jumps to the front of the queue to pick immediately,” Standley informs. “Its hard to get the balance between collection orders and ones for delivery. An unique balance is achieved.”
The new system includes Koerber WMS, voice tech, modules and middleware, plus the four Kardex Megamat carousels (pictured) that were already in use at the DC. The picker no longer needs to input part numbers on the carousel’s control panel. This is a no-touch solution thanks to the Koerber API ordering items in batches. Quite a lot of work was done by Koerber in achieving this interface. “We did have two staff per machine,” Standley continues, “now one person goes to it (and says ‘Ready’) when around 30 orders are ready. So they can go, pick elsewhere and come back. There’s less walking involved.”
What about fast-moving items and stock location? “We wanted accuracy. Quality was paramount.” Standley emphasised. “Phase 2 of the project will take us further, handling inbound products from suppliers and maybe having a dedicated area for fast-movers. We’re also looking at same-day delivery options.”